Market Research Future (MRFR) has published a cooked research report on the “Global Prefabrication Market”that contains information from 2019 to 2032.
The Global Prefabrication Market is estimated to register a CAGR of 5.62% during the forecast period of 2024 to 2032.
MRFR recognizes the following companies as the key players in the Global Prefabrication Market— Riko Hiše d.o.o., RED SEA INTERNATIONAL, Lendlease Corporation, LARSEN & TOUBRO LIMITED, Guerdon, LLC, Barratt Developments PLC, Skanska, Clayton, Daiwa House, Morton Buildings, Inc.
Prefabrication Market Highlights
The Global Prefabrication Market is estimated to register a CAGR of 5.62% during the forecast period and is estimated to reach USD 3,47,846.2 Million by 2032.
The global prefabrication market is experiencing substantial growth due to the increasing demand for cost-effective construction methods. The construction industry is increasingly utilizing prefabrication as a solution to address the demands of efficiency, pace, and budget in an era where these factors are of the utmost importance. Traditional construction methods frequently involve extended timelines, substantial labor costs, and the possibility of unforeseeable expenses as a result of weather delays, on-site errors, or material wastage. Prefabrication resolves these obstacles by relocating a substantial portion of the construction process to a controlled factory setting, where components are manufactured with precision and consistency prior to on-site assembly.
One of the primary benefits of prefabrication is its capacity to decrease the overall cost of construction. Companies can reduce the cost per unit by manufacturing building components in volume, thereby achieving economies of scale. This cost reduction is especially advantageous for large-scale undertakings, as the savings can be substantial. Additionally, the factory-controlled environment enables more effective resource management, thereby reducing the necessity for costly on-site labor and mitigating waste. The capacity to complete projects with fewer workers is a significant advantage, further contributing to the cost-effectiveness of prefabrication, as labor shortages are becoming an increasing concern in many regions.
The restricted design flexibility is a substantial constraint in the global prefabrication market. This restriction affects a variety of sectors, with a particular emphasis on commercial and institutional non-residential Materials, such as healthcare facilities, that necessitate solutions that are highly adaptable and customized. Prefabrication is the process of producing construction components in a factory and subsequently assembling them on-site. Although this approach provides numerous benefits, including potential cost savings and a shorter construction timeline, it also has restrictions on design flexibility. Throughout the construction process, architects and engineers are afforded a greater degree of flexibility to modify and alter designs in traditional construction. Nevertheless, prefabrication typically necessitates a more rigorous design approach. Modifications are both time-consuming and expensive once components have been manufactured, as they must be performed in the factory. The challenge of limited design flexibility is underscored by the trend of increasing customization demands, particularly in sectors such as healthcare, where facilities necessitate specialized layouts and adaptable spaces. For example, healthcare facilities frequently must adjust to the altering needs of patient care and the advancement of medical technologies. The inherent design constraints of prefabricated modules may make it difficult for them to satisfy the evolving needs of the market despite their efficiency.
To resolve this issue, certain organizations are investigating modular systems that provide greater adaptability. These systems enable a certain level of customization within the prefabrication paradigm, including modular wall panels and adaptable interior components. Nevertheless, the capacity to completely adjust to the intricate and dynamic design requirements continues to be a challenge. Furthermore, architects, engineers, and prefabrication manufacturers will probably collaborate more extensively. It may be feasible to develop prefabricated components that provide enhanced adaptability and customization capabilities by early involving all stakeholders in the design process. Nevertheless, the ongoing technological advancements and collaborative approaches are expected to alleviate this challenge in the future, despite the fact that the limited flexibility in design remains a significant restraint. The industry is progressively transitioning to solutions that strike a balance between the necessity for customized, adaptable designs and the efficiency of prefabrication, particularly in sectors that necessitate specialized construction solutions.
Access full report @ https://www.marketresearchfuture.com/reports/prefabrication-market-40366
Segment Analysis
The Global Prefabrication Market has been segmented based by Product Type, by Material, by Construction Type, By Prefabrication Form, by Application.
By Application, the market is segmented into Residential and Non-Residential. The utilization of prefabricated construction methods in the construction of residential structures, including residences and apartments, is referred to as "residential" in the global prefabrication market. Prefabrication is the process of assembling a variety of building components in a controlled environment off-site and subsequently transporting and installing them at the construction site. The numerous benefits of this method, such as reduced construction time, cost savings, enhanced quality control, and environmental benefits, have led to its increasing adoption in residential construction.
The global prefabrication market has experienced substantial development as a result of the widespread implementation of prefabrication in the residential sector. There is an urgent requirement for construction methods that are scalable, cost-effective, and efficient, particularly in swiftly growing economies, as urbanization accelerates and housing demand increases. Prefabrication addresses these requirements by providing construction timelines that are shorter than those of conventional on-site methods. In regions that are experiencing housing shortages, the capacity to promptly deliver substantial quantities of residential units is crucial.
Furthermore, prefabrication is particularly advantageous in markets where skilled labor is either scarce or costly, as it reduces labor costs. The quality and durability of residential buildings are also improved by the precision of factory-produced components, which reduces maintenance costs and extends the tenure of structures. Additionally, prefabrication is inherently more sustainable due to its ability to integrate energy-efficient materials and designs and its reduced waste generation, which is consistent with the increasing global emphasis on green construction practices.
Regional Analysis
The report on the Global Prefabrication Market has been segmented based on region as North America, Europe, Asia-Pacific, Middle East & Africa, and South America. The prefabrication market in North America is undergoing substantial development, which is being fueled by a combination of technological advancements, labor shortages, and the growing demand for sustainable construction practices. The construction industry in the United States and Canada is progressively transitioning to modular and prefabricated building solutions. These solutions provide improved quality control, reduced waste, and faster project timelines. This change is especially apparent in urban areas, where the high demand for residential and commercial spaces necessitates the implementation of more efficient and expedited construction methods.
The ongoing labor scarcity in the construction industry is one of the primary factors driving the prefabrication market in North America. Skilled labor is becoming scarcer, resulting in increased labor costs and project delays. The use of prefabrication facilitates the completion of a greater amount of construction work in controlled factory environments, thereby reducing the necessity for on-site labor and allowing for the automation of tasks. This mitigates these issues. This method not only expedites construction but also reduces the likelihood of delays caused by inclement weather, which is prevalent in numerous regions of North America.
The prefabrication market in the region is also experiencing significant development as a result of technological advancements. The precise planning and execution of prefabricated components are facilitated by the integration of Building Information Modeling (BIM) and advanced manufacturing techniques. This precision results in improved construction quality and minimizes material waste, which is consistent with the increasing emphasis on sustainability in the construction sector. Furthermore, the implementation of green building certifications, including LEED (Leadership in Energy and Environmental Design), is motivating developers to investigate prefabrication as a method of enhancing energy efficiency and minimizing the environmental impact of their projects.
Key Findings of the Study
- The Global Prefabrication Market is expected to reach USD 3,47,846.2 Million by 2032, at a CAGR of 5.62% during the forecast period.
- The Asia Pacific region accounted for the fastest-growing global market due to the significant industrial infrastructure growth.
Leading companies partner with us for data-driven Insights
Kindly complete the form below to receive a free sample of this Report
Companies Covered | 15 |
Pages | 100 |
Certified Global Research Member
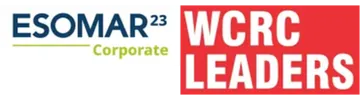
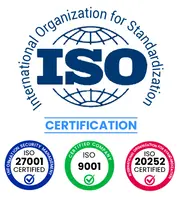
Why Choose Market Research Future?
- Vigorous research methodologies for specific market.
- Knowledge partners across the globe
- Large network of partner consultants.
- Ever-increasing/ Escalating data base with quarterly monitoring of various markets
- Trusted by fortune 500 companies/startups/ universities/organizations
- Large database of 5000+ markets reports.
- Effective and prompt pre- and post-sales support.
Tailored for You
- Dedicated Research on any specifics segment or region.
- Focused Research on specific players in the market.
- Custom Report based only on your requirements.
- Flexibility to add or subtract any chapter in the study.
- Historic data from 2014 and forecasts outlook till 2040.
- Flexibility of providing data/insights in formats (PDF, PPT, Excel).
- Provide cross segmentation in applicable scenario/markets.