Top Industry Leaders in the Liquid Crystal Polymers Market
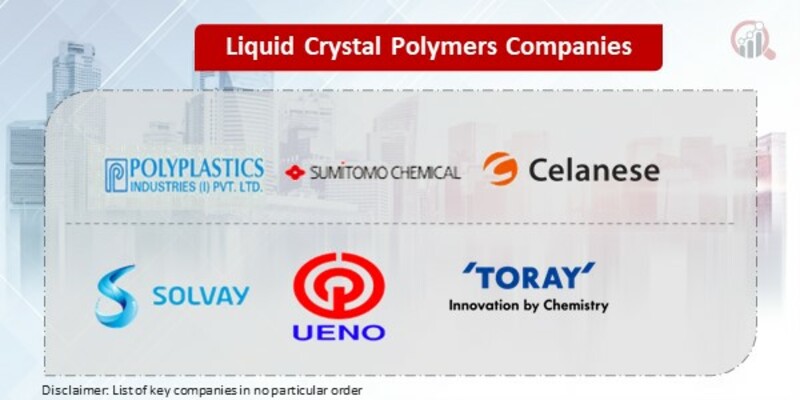
Liquid crystal polymers (LCPs), with their unique liquid crystal alignment and inherent properties, shine brightly in a diverse range of applications. From electronic circuits and automotive parts to medical devices and aerospace components, LCPs offer exceptional thermal stability, chemical resistance, and dimensional precision, propelling them to the forefront of a thriving global market. Let's delve into the strategic maneuvers, influential factors, and recent advancements shaping this dynamic scene, where giants illuminate market share alongside nimble innovators.
Strategies Sparking Growth:
-
Technological Twists: R&D labs are ablaze with advancements. Sumitomo Chemical is pioneering high-flow LCPs, enabling faster injection molding and increased production efficiency, while companies like LG Chem are developing LCPs with improved flame retardancy, catering to stringent safety regulations.
-
Sustainability Focus: Green hues are trending. Companies like Celanese Corporation are investing in research and development of bio-based LCPs derived from renewable resources like corn oil, aligning with eco-conscious customers and regulations.
-
Product Diversification: Leading players like Polyplastics are going beyond standard injection-grade LCPs to develop specialized variants for niche applications like high-frequency printed circuit boards and microfluidic devices.
-
Regional Expansion: Asia-Pacific, with its booming electronics and automotive industries, holds immense potential. Companies like Jilin Chemical Industry Group are setting up production facilities in this region to capitalize on the local demand.
-
Strategic Partnerships: Collaboration illuminates synergy. For instance, Evonik Industries partnered with a medical device manufacturer to develop customized LCPs for implantable devices, expanding both companies' reach and capabilities.
Factors Dictating Market Share:
-
Performance Prowess: Superior heat resistance, chemical inertness, and dimensional stability are crucial metrics. Established brands like Merck KGaA have built reputations for consistent performance, attracting loyal customers in demanding applications.
-
Cost-Effectiveness: Price remains a critical factor, particularly in mature markets. Chinese manufacturers often offer lower prices, challenging established players to optimize production and pricing strategies while maintaining quality.
-
Regulatory Landscape: Stringent regulations on hazardous materials and end-of-life disposal dictate industry practices. Players who comply with these regulations, like Asahi Kasei with its closed-loop recycling systems, gain a competitive edge.
-
Application Diversity: Catering to diverse industries offers resilience. Companies with broad product portfolios like Solvay benefit from diversification, mitigating risks in saturated segments.
Key Players:
- Polyplastics Co Ltd.
- Sumitomo Chemical Co.Ltd.
- Celanese Corporation
- Solvay S.A.
- Ueno Fine Chemicals Industry Ltd.
- Toray International Inc.
- SAMSUNG FINE CHEMICALS CO. LTD
Recent Developments:
September 2021, Polyplastics Co. Ltd announced the construction of a new polymerization facility with a 5,000-tonne-per-year capacity at Polyplastics Taiwan Co. Ltd. This new polymerization equipment for PTW enables the whole fabrication of LCP goods, from polymerization through compounding. With the expansion of PTW's LCP polymerization facility, the Polyplastics Group will eventually attain a production capacity of 25,000 tons/y of LCP polymerization.
September 2021, Polyplastics Corporation announced the release of a new product. In addition, this corporation is constructing a new polymer facility in Taiwan. As a result of this, market production is likely to increase. The company will produce around 5,000 tons of polymer crystals.
March 2020, Solvay, a renowned provider of specialty polymers, announced the development of a new LCP grade specifically tailored for use in high-voltage automotive applications. The new Ryton R-4-240NA LCP grade has good electrical qualities such as high dielectric strength and low dissipation factor, making it perfect for use in electric vehicle components such as connections, sensors, and battery management systems.